Job Opportunity at Britannia Industries Limited
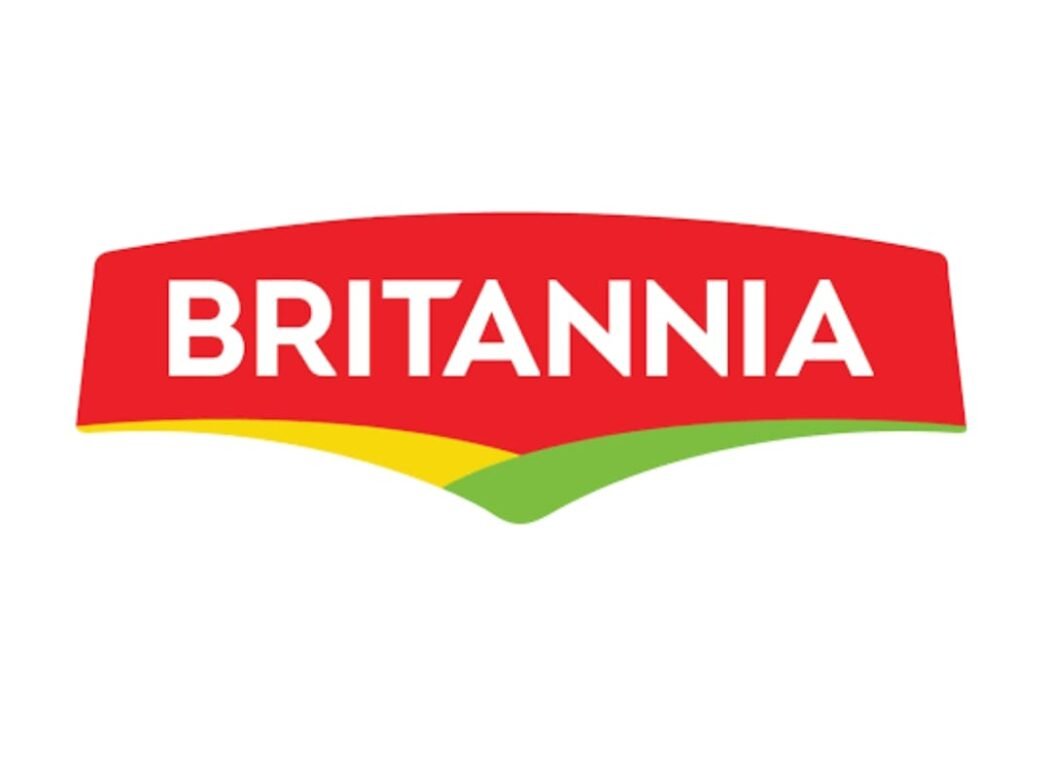
Job Opportunity at Britannia Industries Limited
Position: Quality Assurance Officer
Location: Nawabganj, Uttar Pradesh, India
Job Description:
Position Title: Quality Assurance Officer
Function: Quality
Educational Qualification: Graduate in Food Technology/MSc. Chemistry
Experience: 3-5 years in Quality Assurance
Desired Competencies:
- Familiarity with quality management tools and methodologies.
- Basic knowledge of applicable software for statistical data.
- Negotiation skills and customer orientation.
Key Responsibilities:
Quality & Food Safety Execution:
- Monitor product quality online, taking immediate action through production officers and CP management for any non-conformity.
- Test finished goods with standard sampling methods and proper documentation.
- Participate in regular product quality exercises.
- Verify process records, ingredient shelf-life records, and in-process quality check records periodically.
- Ensure compliance with hygiene, food safety, and GMP requirements during manufacturing.
Statutory Compliance:
- Check wrappers for correct addresses, MRP, veg logo, and mandatory declarations.
- Conduct random sampling for pack weights at different production stages.
- Ensure functioning of coders and compliance during changes in date, shift, and supervisor’s name.
- Calibrate weighing balances and dead weights as per schedule.
Consumer Complaints:
- Share and identify causes of complaints with CP management, supervisors, operators, and shop floor workers.
- Design corrective and preventive measures, implementing them immediately.
- Evaluate action effectiveness through regular process and product evaluations.
- Analyze and share complaint data with CP management for improvement plans.
Benchmarking:
- Visit retail outlets and distribution points weekly to understand customer and consumer quality concerns.
- Evaluate competition products for improvement opportunities and share action plans for enhancements.
- Measure effectiveness through market evaluation and customer feedback.
Process Improvement Initiatives:
- Identify and prioritize improvement opportunities in system, process, cost, and time in consultation with operations and quality.
- Periodically review overall quality improvement at the factory.
Management Information System:
- Send periodic summary reports on factory quality performance to the quality manager.
- Communicate critical quality and food safety concerns to relevant stakeholders as soon as observed.
Outcomes Expected:
- Compliance to standards.
- Packs and products complying with statutory requirements.
- Reduction in the number of complaints.
- Consistent and superior quality products.
- Periodic performance reports on factory quality.
If interested, please apply with your updated resume.